Manual Handling Operations Regulations
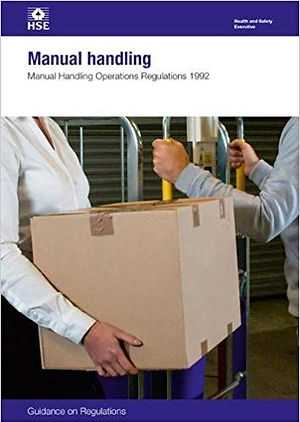
The Manual Handling Operations Regulations were updated in September 2016 with the L23 (4th Edition). To download the updated regulations click the PDF at the bottom of this page.
​
The Manual Handling Operations Regulations 1992, as amended by the Health and Safety (Miscellaneous Amendments) Regulations 2002 set out guidance to help you manage, control and reduce the risk of injury from manual handling.
​
The Regulations apply to manual handling activities involving the transporting or supporting of loads, including lifting, lowering, pushing, pulling, carrying or moving loads. Loads can vary such as boxes, sacks, trolleys and other inanimate objects but also relate to the moving of animals and people.
​
All sorts of workplaces have manual handling risks, such as factories, warehouses, farms, dairies, building sites, offices, schools/ colleges, hospitals and while making deliveries. The Labour Force Survey estimates that work-related musculoskeletal disorders (MSDs) account for around 40% of all work-related ill health. Evidence shows that, as well as manual handling, heavy manual labour, awkward postures and a recent or existing injury are all risk factors in the development of work-related MSDs and manual handling lost time accidents.
You can help to reduce the risk of manual handling injuries by taking the following steps:
​
-
Comply with the Regulations and guidance
-
Regularly review risk assessments
-
Encourage early reporting of symptoms by workers
-
Effective management of any manual handling injuries
-
Consult and engage the workforce and their representatives
What do I need to do?
​
-
Avoid the need for hazardous manual handling, ‘so far as is reasonably practicable’;
-
Assess the risk of injury from any hazardous manual handling that can’t be avoided;
-
Reduce the risk of injury from hazardous manual handling, ‘so far as is reasonably practicable’.

Avoid:
​
-
Do the loads need to be handled or can you work in a different way?
-
Can you automate the process, for example robots, powered conveyors?
-
Can you use mechanical aids to remove the manual element, for example a crane or other lifting equipment, powered pallet trucks/stackers, forklift trucks?
​
Assess:
​
When looking at an operation consider the task, the individual capability, the load and the environment it takes place, together with other factors including psychosocial factors and the relationship between them.
​
The Regulations contain useful risk assessment filters in the Appendix which help you decide the right level of detail needed as part of the risk assessment process. You can then use recognised tools from the HSE’s MSD Toolkit, such as the MAC Tool (Manual Handling Assessment Charts) to assess lifting, carrying and team handling, the RAPP Tool (Risk Assessment Pushing and Pulling) to assess pushing and pulling operations, or the ART Tool (Assessment of Repetitive Tasks of the Upper Limbs) for tasks that require repetitive movement of the arms and hands. If these tools are not detailed enough or you are in any doubt you should complete a full risk assessment. Figure 19 (above right) from the Regulations summarises the process.
​
Reduce:
​
After evaluating the risks:
​
-
You must decide whether the existing precautions are adequate or whether more should be done
-
Record your findings and tell your employees about them
-
Reviewing your assessment and revise it if necessary
At Osteopathic Solutions, our Manual Handling Instructor (Train the Trainer) Assessor Programmes accredited with The CPD Group will equip you with the skills and knowledge to understand the Manual Handling Risk Assessment process, have competency to conduct onsite Manual Handling Risk Assessments and identify practical solutions to lower MSD risk. Attendees will also be taught safer manual handling techniques and be able to design job specific, bespoke manual handling training for your workers. This combined approach will significantly reduce manual handling lost time accidents and workplace MSDs.
Manual Handling Operations Regulations
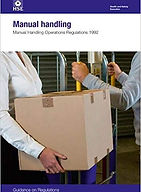
Need to refresh on the HSE's Health & Safety Laws and Guidance regarding Manual Handling Operations? Download by clicking on the PDF to the right above. If you don't have time to update with this document, then simply read through this page's summary above. Please be mindful that guidance on manual handling techniques and safer handling practices is limited in this publication.
Looking for Continual Professional Development regarding teaching safer, job specific Manual Handling practices in your working environment? Want to reduce your Manual Handling Lost Time Accidents? Then click on the Public Manual Handling Instructor Course page. Our Accredited Programme takes only 2 Days of Course attendance to qualify as a Manual Handling Instructor and Risk Assessor.
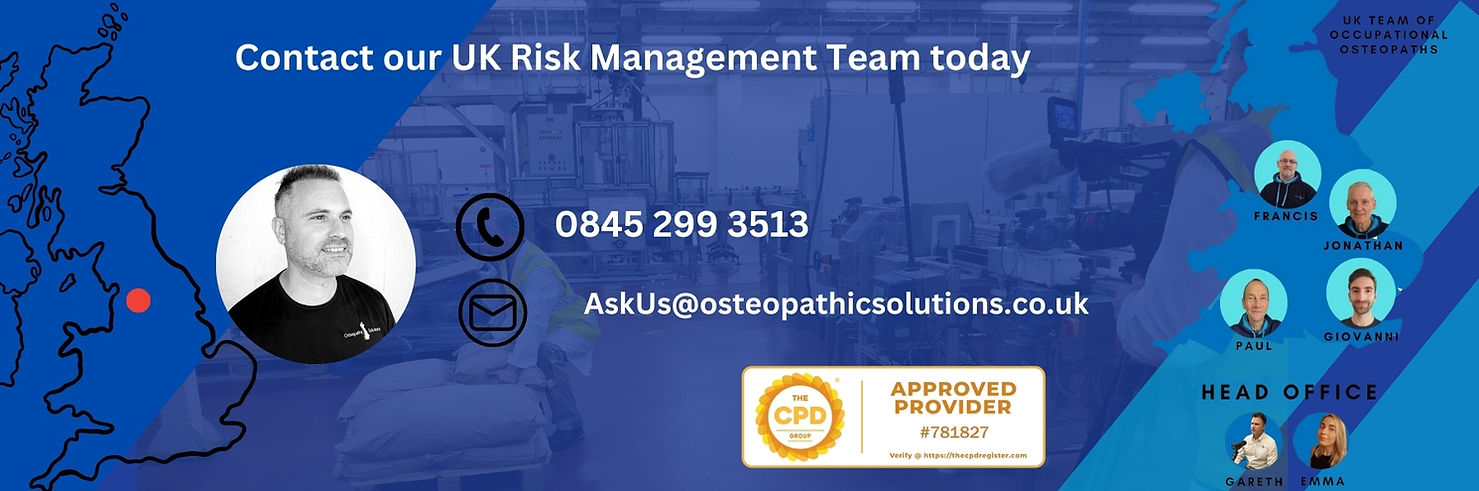